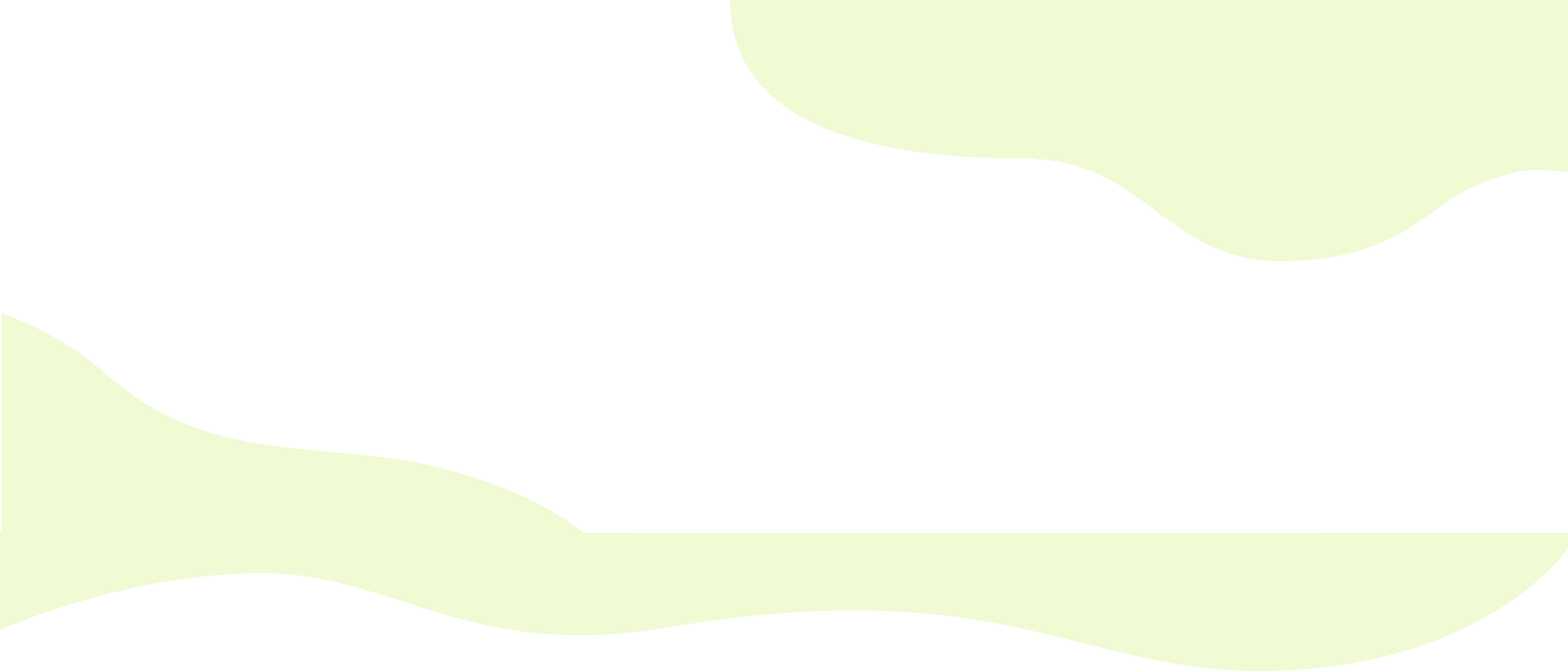
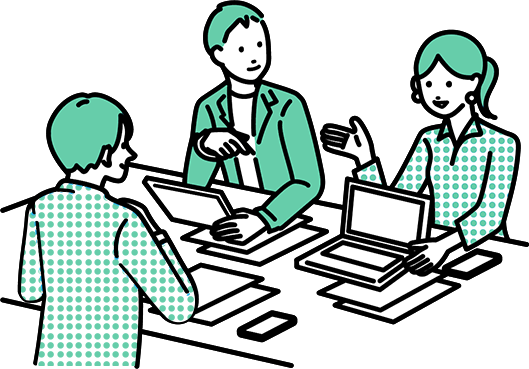
鋳物 ・ 鋳造関連の教育EDUCATION
- ホーム
- 鋳物 ・ 鋳造関連の教育
鋳物・鋳造関連の教育education

こちらでは、鋳造シミュレーションに関係する技術的な背景や、基礎知識、鋳造過程で発生する欠陥(鋳造欠陥)など、鋳造技術にまつわる話を紹介しています。
遠回りになりますが、広い範囲で鋳造の技術の紹介もしているのは、その方が知識として分かりやすくなるからです。
「温故知新」、先人の知恵に学ぶところ、大です。
そして、「知識を正しく使うとき、初めて教育の目的は果たされます」。教育が良心に刻まれてそうして初めて教育の目的が達成されると考えます。
数値解析について
● 数値解と解析解の違い
数値解とは、微分方程式を積分するなどして、関数の形で得られた厳密解のこと。解析解とは、差分法などの数値演算による近似解のこと。
数値解は、変数と解が一目で分かり、関数の形になっているので、式に変数を代入すると解が直ちに求まりますが、単純な問題しか解けません。
一方の解析解は、複雑な問題にも適用できますが、条件が変わるたびに、いちいち計算しなおさなければならないため、一目で分からず、見通しが良くありません。
注目
- ●直観を大切にする
-
出来る限り、解析解を使った方が物理現象に関して、理解が深まります。
また、数値解を使うときでも、解析的に整理が必要です。
- ●シミュレーションに溺れない
-
市販の鋳造シミュレーションソフトは色々な解析が出来て、便利ではありますが、正しく活用するためには計算の内容を理解しておくことが大切です。
研究を目的とする時は市販のソフトでは満足できないのでプログラムが自作できるのが良いですね。
● 数値解の技法について
数値解法には、差分法・有限要素法などがあります。さらにそれらにも、細かく種々の手法がありますが、大まかに言えば、精度や計算速度に大差ありません。
差分法の代表的なものが、陽的差分法と呼ばれるものです。(陰的差分法もあります)
陽的差分法(陽的解法)のことを「前進差分法」。陰的差分法(陰的解法)のことを「後退差分法」とも呼び、陰的解法のには、後退差分法の他にクランク-ニコルソン法(改良オイラー法)もあります。
実際の複雑形状をしたモデルにおいては、差分法はなく、有限要素法、境界要素法があります。
注目
- 差分式の展開(離散化)
-
物理現象→微分方程式→差分式という流れで、数値解を解きます。
差分式にする時の展開の方法にはテーラー展開(有限差分法)などがあります。
厳密な、微分方程式を差分式に変換する技法(離散化)については、コンピュータ伝熱・凝固解析入門(大中逸雄 著)が参考になります。(初めての人には難しいかもしれません)
● 計算領域の定義について
コンピューターを使ってシミュレーションをする場合、計算・解析の対象となる領域をメッシュで切ります。(要素分割とも呼び、オイラー系の手法と呼びます。一方、要素分割が不要のラグランジュ系の手法、例えば、粒子法というものもあります。)
メッシュで切った領域(要素)に、物理的な値(温度など)を持たせて計算しますが、その値を持たせる位置(節点:node)を、要素の中心にするか(内接点)、要素の頂点に設定するか(外節点)で、計算式が変わります。(流動計算の流速は、辺に持たせます)
注目
- ●節点
-
物理現象→微分方程式→差分式という流れで、数値解を解きます。
差分式にする時の展開の方法にはテーラー展開(有限差分法)などがあります。
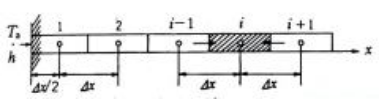
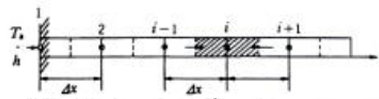
● 鋳造に特徴的な熱の取り扱い(潜熱)
鋳造工程においては、金属が固まります。つまり、液体から固体になるのですが、その時に「潜熱」と呼ばれる熱を出します。これが、特徴です。
純金属は一気に潜熱を放出し、合金はグズグズ液相線と固相線の間で温度低下しつつ放出します。
この過程を数値計算する場合、主に3つの方法で取り扱うことが知られています。
1.温度回復法:純金属に適している。
2.等価比熱法:等価とは「見かけ」の意味で、温度によって見かけの比熱を使う。
3.エンタルピー法(含熱量法):純金属、合金、共晶で同じようなプログラムで扱え、すっきりした形。
注目
- ●含熱量と温度との関係
-
熱力学的な、平衡状態(マクロな視点)では下図のようになる。実際には、過冷却や結晶の核発生、成長など非平衡な状態(ミクロな視点)になる。
● 凝固形式と凝固温度範囲
金属が固まる時に、その形式は主に2つあります。
1.表皮形成型:純金属のように、凝固温度範囲が0か、狭い温度範囲を持つ合金(Skin formation)純銅、アルミニウム、青銅、黄銅、クロム銅など固相・液相が完全に分かれるため、収縮に対する溶湯補給が容易。適当な押湯を設けて欠陥を排除することが容易。
2.かゆ状型(マッシー型):温度範囲の広い合金に見られる凝固形態。りん青銅、すず青銅、洋白(Cu・Zn・Ni,500玉)などは、固相率が50~70%になるとかゆ状になり、生成したデンドライトの樹間に微細な収縮巣(ミクロポロシティ)が発生。冷金か金型を用い温度勾配を大きくとり、指向性凝固させる。Cu-Sn系合金では、かゆ状凝固により収縮巣の発生とSnの偏析、逆偏析が生じる。
注目
- デンドライト凝固
- デンドライト凝固の場合は、ダルシー流れをモデルとして計算しています。(凝固形態を考慮した流動停止)
▼純金属 ▼短い凝固範囲の合金 ▼中位の凝固範囲の合金 ▼長い凝固範囲の合金
1.溶湯(湯先)の温度の低下(固相率の上昇)
2.鋳型内の圧力の上昇(背圧)
などを見るのが普通ですが、JSCASTでは、右の図のように金属の種類によって、さらに詳しく評価できるようになっています。(純金属、鋳鉄、合金で凝固形態が異なるため、凝固形態を選択できます)
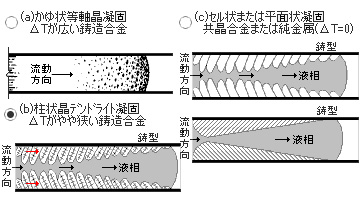
差分法について
● 差分式の精度と、風上差分と中心差分
テーラー展開を打ち切る際に、⊿Xのオーダーで打ち切る場合を、1次精度、あるいは、差分近似のオーダーは1次であると表現し、⊿Xの2乗の項を2次精度であると表現します。
Xの関数のφ(X)を考える場合、Xの前後の関数値φ(X-1)、φ(X+1)を使う場合を中心差分と呼び、Xの値であるφ(X)と、Xの後の関数値、φ(X-1)を使う場合を後退差分と呼び、後退差分を使う方法を風上差分と呼びます。風上差分は、中心差分を安定させる目的で使います。
1次精度の後退差分を用いた場合、1次精度風上差分スキームという表現をします。
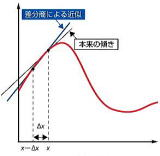
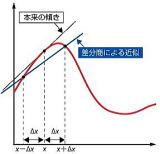
● 陽解法と陰解法
空間と時間が同時に変化する時、横軸に空間(X)、縦軸に時間(t)をとり、時間tにおける座標(Xi)と、その前後の値から、未知の時間t+⊿tにおける座標Xiの値を求めるのが陽解法です。
一方、時間tにおける座標(Xi)と、その前後の値、そして、未知の時間t+⊿tにおける座標Xiの前後の値から、時間t+⊿tにおける座標Xiの値を求めるのが陰解法です。
陰解法の法が計算が複雑になりますが、⊿tの値を大きく出来るので、結果が早く出る(収束すると表現する)ことが、多々あります。
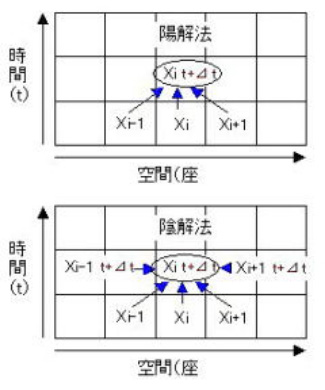
● 連立方程式の解法
例えば流れの計算の場合、運動量保存則(ニュートンの第二法則を変形したもの。流体ではナビエストークスの式とも呼ぶ)と、質量保存則(セル内の物体の質量の情報)を連立させた微分方程式を解きますが、実際にパソコンで計算させるためには差分式にして、つまり、運動量保存則の差分式(主な未知数は、速度、圧力等)質量保存則の差分式(主な未知数は速度等)を解きます。(方程式の概要は、便利な操作説明書にもあります)
2つの保存則の式で共通して未知数である速度を消去するように連立させた差分式(主な未知数は、圧力)を圧力方程式と呼びます。(右の上段のn個の式)
計算するセルがn個有るとすると、連立させた差分式もn個有り、マトリックスにして一度に解くことになります。例えば、SOR法などを使って解きます。
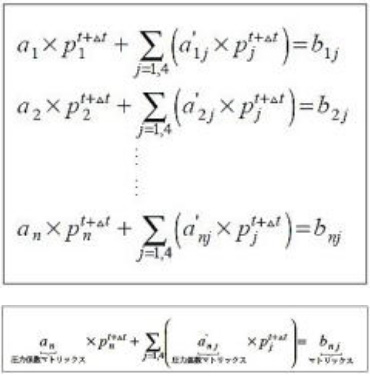
鋳造設計の基本
● 合金のデンドライト凝固
多くの実用材料は合金です。純金属と異なり、通常、合金の凝固界面は不安定で、G(固液界面での温度勾配)とV(結晶成長速度)が小さくなるに従い、結晶の先端が突起してきます。熱の流れ方向に加え直角方向にも凹凸が生じた結晶がデンドライトです。(界面が荒れる場合、ノンファセット凝固とも言う)
固液界面が荒れた時にデンドライトの形になります。半導体のシリコンやゲルマニウムのように平滑な固液界面の場合は、リボン状結晶になります。(界面が平滑な場合、ファセット凝固ともいう)
金属とシリコン(非金属)合金の場合「共晶」になり、組み合わせとして考えられるのは、下記の3つです。
1.ノンファセット/ノンファセット(Ni耐熱合金など)
2.ノンファセット/ファセット(Fe-C系、Al-Si系)
3.ファセット/ファセット(セラミックなので割愛)
注目
- ●鋳鉄
-
Fe-C系の代表的な材料、鋳鉄では、通常は組織中にデンドライトは見えませんが、晶出した黒鉛(C)の形に眼がだまされて見えないだけで、凝固中に液相を覗くと見えます。
▼(a)→(b) →(c) → (d) → (e) でG/Vが小
▼デンドライトが太り、等軸晶、柱状晶に
鋳造シミュレーションの歴史
● 歴史
1960年代から凝固解析について研究されるようになり、1980年代初頭から普及し始めました。湯流れ解析については、Los Alamos 科学研究所などの研究機関で研究が開始され、1983年ピッツバーグ大学のW.S.Hwang、R.A.Stoehrらが、その成果を鋳造プロセスにおける溶湯流動過程に応用しています。その後の研究・開発によって、1999年頃には普及し始めており、今日の鋳造シミュレーションは実用的な品質予測のツールとして認知されてきています。JSCASTはパイオニアの一つです。
鋳造プロセスへのCAEの適用は、1960年代までさかのぼり、大型鋳鋼品の電熱解析から凝固解析を可視化するために利用されました。湯流れ解析は、流れの基礎方程式が凝固解析に比べると格段に複雑で、解析時間も膨大であることから、1980年代になりようやく着手されました。2000年以降は、パソコンでのCAD/CAMシステムの連携が進んだことから、モデルのメッシュ作成の負荷が激減し、普及が加速した経緯があります。
コンピューター上での仮想実験(シミュレーション、CAE)は、手書きの製図作業がパソコン上でのCADに置き換わることで、CAE・CADの統合が進み、発展しています。1950年代には、CAEは大変高価で、専門家だけが扱うブラックボックス的な面がありましたが、その後、差分法、有限要素法、境界要素法などの数値解析法を用いた様々なプログラムが開発され、適用領域もパソコンの性能と共に拡大していきました。(頂点モデル→ワイヤーフレームモデル→サーフェイスモデル→ソリッドモデルへと進化)
RP(Rapid Prototyping)という3DのCADで作成された形状データーから、現物の立体モデルを製造する手法も1980年代に光硬化性樹脂も用いた光造形法が発表されたのをきっかけに開発が進められ、3Dプリンタと呼ばれる積層造形機の特許、2007年に切れたために10万円台の安価な3Dプリンタが出回り、急速に普及し出しています。
● 基礎式について
連続の式(質量)、運動量保存式(速度)、エネルギー保存式(温度)の3つが基本です。
粘性を考慮した運動方程式がナビエ-ストークス方程式です。(N-S方程式)また、圧力を含めた、状態式を4つ目に加えることもあります。2成分以上から成る系では、拡散方程式を解くことになります。これらは偏微分方程式で記述されています。
x,y,zの直交座標系では、通常、時間を独立変数とし、速度、圧力、温度、濃度を従属変数(時間によって変化する)としていますが、従属変数を空間に固定された座標によって定義する表し方を、オイラー表示、各粒子ごとに定義する表し方をラグランジュ表示と言います。流れの場を解く場合は、任意の場の情報が必要なので、オイラー表示が都合が良いです。基礎式の導出は、分かりやすい直交座標系(x,y,z)を使うことが多いのですが、他の座標系へと変換する便宜性も考慮し、テンソル形式で併記されることもあります。
物理現象に対し、実際の物理モデルでなく、数学モデルは主として連立微分方程式によって構成されますが、実際に興味ある現象を予測することは困難で、限られた範囲のものしか解くことは出来ません(厳密解)。対象領域全てではなく、領域内の離散した格子の情報を得る、数値解法がパソコンの発達と共に強力な手法として採用されています。数値解法の場合、微分方程式ではなく、代数方程式を使うので簡単になります。実験と違って、低コスト、所要時間が短い、という利点があります。しかし、適切な数学モデルでなければ無意味です。
● 基礎式の表示について 基礎式は、それぞれ積分表示と、微分表示とがあります。一長一短です。歴史が古いのは微分表示で、積分表示は、有限体積法や有限要素法です。
鋳造シミュレーションの技術
● 数値計算法
基礎式を満足する数値を求める有限差分法(FDM)と、基礎式を満足する解の近似式を求める有限要素法(FEM)、境界条件を満足する解を求めるのが境界要素法(BEM)です。
数値解析は、個展的な応用数学(微積分を用いて定式家)と現代応用数学(離散数学)の接点にあります。計算の効率(手間と精度)を考慮に入れてプログラムを組みます。誤差には打ち切り誤差(無限を有限化)と、まるめの誤差(無限小数を有限桁にする)があります。古典的数値解析の中心課題に補間というものがあります。コンピューターが発達した現在では、古典的な凝った補間法が必要なのは比較的まれですが、数値積分・数値積分・常微分方程式の数値積分などの古典的な解法は補間公式から直接導くことが出来ます。
代表的な補間法に、ラグランジュ(Lagrange)補間、有限差分(Newtonの前進・後退公式、Gaussの前進・後退公式)などがあります。
● 各数値解析の特色 有限差分法(FDM)は、複雑な形状のものは難しく、有限要素法(FEM)は、熱流体現象の直接的な理解には不向き、境界要素法(BEM)は基礎式が特殊な場合に限られます。
● 基礎式の離散化
物理現象を表現している微分方程式を、離散化方程式に誘導する(差分法か有限要素法)方法はいくつかあります。代表的なものに、テーラー級数を用いる方法、変分法、重みつき残差法(ガラーキン法)、コントロール・ボリューム法(理解しやすい)などがあります。なお、コントロール・ボリュームの界面の取り方は格子点の位置関係でいくつか方法があります。
コントロール・ボリューム法は、通常、直交座標を使います(フランスの哲学者のデカルト「Des Cartes」にちなんで、なので、カーテシアン座標とも呼ぶ)が、二次元極座標のように、どのような直交座標系でも使えます。
速度成分に対しては、スタッガード格子がよく使われます。スタッガード格子は最初、1965年にMAC法によって使われ、1972年のSIVA法、SIMPLE法の基礎になっています。
基礎式を数値解析するために離散化し、連立方程式を解きます。未知数が時間のみの陽解法、未知数が空間、時間にまたがる陰解法があります。陽解法、陰解法、それぞれ、離散化は、前進オイラー法(オイラー陽解法)、後退オイラー法(オイラー陰解法)とよばれます。解の収束性については、陽解法よりも陰解法の方が解が安定になります。なお、陽解法と陰解法の間に、クランク・ニコルソン法があり、多くの条件で安定しています。常微分方程式の数値解析は、テーラー(Taylor)級数を用いる方法の他、ルンゲ・クッタ(Runge-Kutta法)が用いられます。
流れの場を計算するアルゴリズムについては、大きく分けて2つあります。1つ目はMAC(Marker-and-Cell)法に基づく系統(陽解法)であり、2つ目はSIMPLE(semi-implicit method for pressure linked eqation)法に基づく(半)陰的な解法です。また、MAC法を簡略化したSMAC(Simplified MAC)法や、MAC法で解いた圧力に関するポアソン方程式をニュートン法で解くHSMAC(Highly Simplified MAC)、或いはSOLA(solution algorithm)法もあります。SIMPLEを収束性が上がるように改良したのが、SIMPLER法(SIMPLE Revised)です。
流体の流れによって、対流が発生します。対流項(そして拡散項)を計算する場合、中心差分で解くのは不向きの場合があります。その解決法として、風上差分、解析的に解く、厳密解(指数法)、ハイブリッド法、べき乗法などがあります。
● 方程式の解法
連立方程式は、Gauss-Seider(ガウス-ザイデル)法、SOR法、共役勾配法等で解きます。
分類として、直接法(LU分解、ガウスの消去法、Gauss-Jordan(ガウス-ジョルダン法))、間接法(ヤコビ法、ガウス-ザイデル法、SOR法(Successive Over-Relaxation)の二つがあります。その他、クロリフ部分空間法(共役勾配法、共役残差法、安定化双共役勾配法(Bi-CGSTAB))があります。
直接法は、丸め誤差がなければ厳密解を得ることが可能ではありますが、格子の数の行列を使う大規模な計算となるので、必要なメモリーが膨大になり、計算時間もかかるので、実用的ではありません。そこで、偏微分方程式を差分法によって離散化して解くことになります。
ガウスの消去法を発展させたのがLU分解で、有限回数の演算で解を求めることが出来ますが、係数マトリクスの次元が大きくなると、大きなメモリー、多数の演算回数が必要となり、計算時間が膨大になります。一方、連立方程式の解を修正しながら解を求める方法があり、反復法と呼ばれます。効率的に解を求めることができます。
有限要素法で用いられる反復法としては、共役勾配法が代表的で、並列計算処理も可能となって、効率的に解を得られることが期待できます。
方程式を直接法(TDMA:三重対角行列アルゴリズム)で解くと、かなりのメモリー量と時間が必要となりますので、反復法を使います。反復法には、一番簡単な、ガウス-ザイデル法の他に、SIP法(StronglyImplicit Procedure)などがあります。直接法とガウス-ザイデル法を組み合わせた線順法も知られています。
● CAEを利用した計算の流れ(モデルの構築を観察に合うまで繰り返します)
3Dモデルの作成 → メッシュ分割 → 条件設定 → 計算 → 結果出力 → 評価 → (思わしくない場合は、形状の変更、条件の変更を繰り返し) → 完了、です。
A.メッシュ分割:有限要素法(FEM)、差分法(FDM)に大別されます。(メッシュの不要な粒子法も出てきています)FEMは形状の再現性、解析結果の精度は良いが、解析モデルの作成が難しいという欠点もあります。FDMは、解析モデルの作成が容易、計算速度も速いのですが、形状再現性と、解析精度に難があると言われています。FEMでも、メッシュをうまく作成しなければ、良い結果を得ることが出来なくなります。(大事ですが、見落とされています)
B.条件設定:金属の密度、動粘性係数などの物性値、溶湯や金型の温度の初期条件、溶湯/金型間の熱伝達係数などの境界条件、溶湯の解析条件を設定しますが、あまりに現象に忠実にしようとすると、解析が複雑になり、計算時間が長くなり、計算が収束しなくなる(発散する)ので、目的に合う条件設定をします。
C.計算:計算を行う部分は、ソルバーと呼ばれます。湯流れと凝固解析を一緒に計算する連成解析や、組織予測、熱応力解析など、様々なソルバーがあります。凝固欠陥の予測法には、主に等温度法、G/√R法、直接シミュレーション法(定量予測も可能。マクロひけ巣、ざく巣などの位置と大きさまで正確に予測可能)があります。弾塑性解析(Elastic-Plastic Analysis)も可能です。
D.結果の出力:数値解析結果を、可視化する部分で、ポスト・プロセッサと呼ばれます。湯流れ解析の場合は充填状況や速度分布、凝固解析の場合、温度勾配、凝固時間などが表示されます。
E.評価:実際の欠陥の発生位置と湯流れ解析の結果を照合します。具体的には最終充填部の位置、湯境やガス巻き込み(ブローホール)の関連の検討などです。ポロシティの位置や定量分析などの評価もJSCASTで可能です。
F.繰り返し(形状、条件変更):解析結果を参考に、モデル形状、条件、要素サイズなどを変更し、再解析します。自動化(AI)の適用が検討されています。
G.解析の種類:湯流れ解析(湯境、ガス欠陥(ブローホール))、凝固解析(引け巣の発生の予測には、等固相率法、等温度法、凝固時間法、温度勾配法)、変形、金型温度解析(焼きつきの発生を予測する)などがあります。
鋳造シミュレーション(CAE)に対する不満は、1位予測精度(29%)、2位欠陥判定基準(26%)という統計があります(2006年度鋳造CAE研究部会)。この傾向は、性能が上がった現在(2018年)でも変わらないようです。
ダイカストでは、品質や生産性の50%が製品形状、30%が鋳造方案で支配され、残り20%が鋳造条件(作業を含む)だと言われます。また、ダイカストは製品形状を含めた金型で80%が決定するとも言われます。
鋳造方案について
● 優れた鋳物製造のために必要な10のルール(John Campbell教授)
1.良い溶湯の準備
2.湯面の乱れをなくすこと
3.表面酸化物の取り込みをなくすこと
4.気泡の取込をなくすこと
5.中子ガスを逃すこと
6.引け巣対策(押湯設計)
7.溶湯の対流防止
8.偏析防止
9.残留応力の低減
10.寸法基準点の正しい設定
上記のうち、2~7までが鋳造方案に関係するもの。鋳造欠陥の8割は注湯時の湯面の乱れによるものです。
参考図書:「基礎から学ぶ鋳造工学」(日本鋳造工学会)
● 鋳造方案
鋳造品を製作するための生産設計を「鋳造方案」と呼びます。
鋳鉄などでは、冷却速度が早過ぎるとチルや割れ等の欠陥が生じやすく、アルミニウム合金では、冷却速度が早い方がポロシティ欠陥が発生しにくいです。
● 方案に正解はない
1.堰の設置位置
2.湯道の形状(湯流れの方向性)
3.押し湯のサイズ、位置
4.湯口、湯口底、湯道
(断面積など 湯口:湯道:堰総断面積)
● 方案の自動設計の注意点(ソフトを信じてはいけない)
シミュレーションソフトの自動設計に慣れると、最終充填部・最終凝固部しか見ないようになる傾向があります。
現象のメカニズムの理解し、過程が分からないといけません。
そのためにも、特に商用の鋳物の場合は、ミニマムコストが要求され、仕上げの様子など(中子と仕上げはコストに関係する)現場を見ないと分からないことも含めて、色々な検討が必要になります。
● 凝固設計について
製品の薄肉部→厚肉部→押湯の順に凝固を終了させます(指向性凝固)
1.押湯の場所と個数有効範囲の表を参考にする
2.押湯の種類と形状
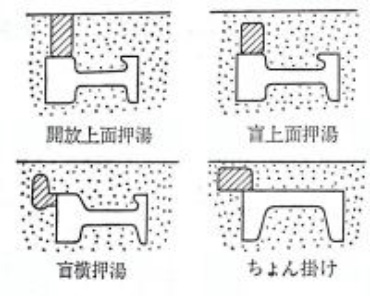
3.押湯の寸法:押湯方程式というものがある。モジュラスM(M=V(体積)/S)を使って凝固時間を表現した、クボリノフの式がある。
4.冷や金の設計:指向性凝固によってホットスポットの位置を変更できる。
5.肉厚こう配による押湯の省略も可能。
参考図書:「大学講義シリーズ24 溶融加工学」(コロナ社、大中逸雄・荒木孝雄 共著)
● 湯口設計について(流動設計) 1.湯口系の種類の選択
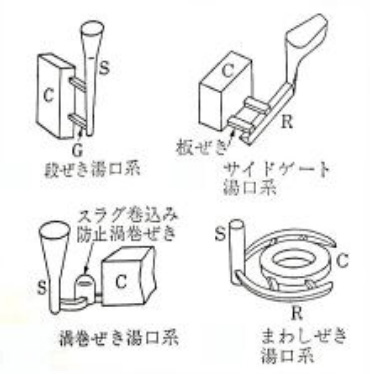
2.湯道、堰の数、位置寸法:溶湯が均等、迅速に流入するようにする
3.湯口比:湯口断面積の設計。加圧方式(鋳鉄系)・非加圧方式(Ai,Mg合金)
4.鋳込速度、鋳込温度:速い→砂かみ、のろかみガス欠陥、鋳型破損
遅い→湯まわり不良湯じわ、照らされ
高い→ガス、ひけ巣欠陥
▼注湯時に生じる鋳型破損の例
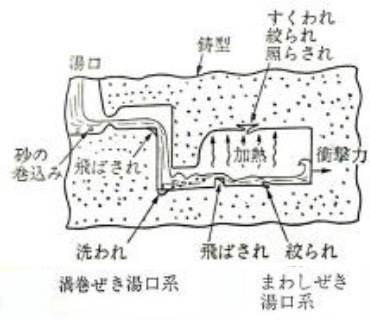
溶湯流により、鋳型の一部が欠ける → 飛ばされ、鋳型の一部がえぐられる → 荒され(洗われ)鋳型と溶湯が反応する → 焼着き
5.ヘッドの有効高さ:有効ヘッドの高さをベルヌーイの式に適用して、湯口比、鋳込時間を使って、湯口系の断面積が決定される
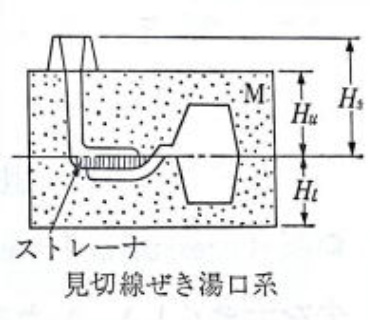
● その他(色々な検討) 仕上げに方案の痕跡を残さない、型バラシしやすい、見切り面の制限、堰の除去・除肉(駄肉の除去)、歩留まり向上など。
鋳造欠陥について
● 凝固欠陥として
1.ミクロ偏析
2.マクロ偏析(正偏析・負偏析、正常偏析・逆偏析、V偏析逆V偏析・A偏析)
3.気孔欠陥(ガス気孔欠陥、ひけ巣欠陥)
4.高温割れ
5.その他の欠陥(組織欠陥、介在物欠陥、高温変形)
などがあげられます。ここでは特に「気孔欠陥」についてとりあげています。
SEM(走査型電子顕微鏡)を使って、欠陥内部の拡大画像が得られ、やEDS(エネルギー分散型X線分析)を使って、成分の分析をします。
鋳造欠陥の名前、鋳造法、金属の種類、要因、対策の順番で書いてあります。
(対策は方案で出来るものを優先)
●内引け巣、低圧鋳造、アルミ合金(AC2B) 右は拡大写真。その部位が速く冷却されるようにします。
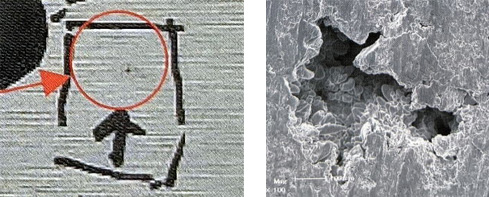
鋳鉄などでは、冷却速度が早過ぎるとチルや割れなどの欠陥が生じやすく、
アルミニウム合金では、冷却速度が早い方がポロシティ欠陥が発生しにくいです。
● 内引け巣、生型、ねずみ鋳鉄(FC300) 中子ガスの発生による欠陥。押湯設計、冷やし金の活用です。
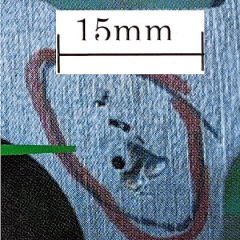
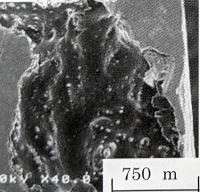
● ざく巣、フルモールド鋳造、球状黒鉛鋳鉄(FCD600) 凝固時の体積収縮による溶湯供給不足、鋳込み温度を上げます。
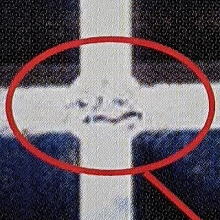
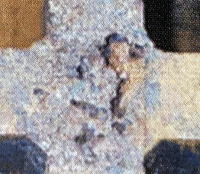
● ざく巣、フルモールド鋳造、球状黒鉛鋳鉄(FCD450)
鋳込み温度が低いと集中型、高いと分散型になります。
(上:1398℃、下:1453℃)
鋳込み温度を低くし、冷やし金を使って指向性凝固させます。
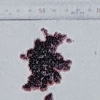
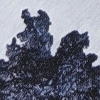
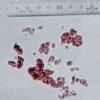
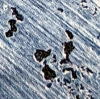
● ガス吹かれ(ブローホール) シェルモールド鋳造、ねずみ鋳鉄(FC250) 粘結剤を減らし、空気およびガス抜きを適切にしました。
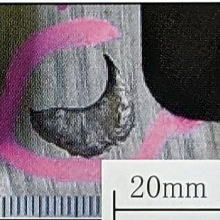
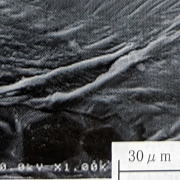
● ピンホール(残渣がスラグ化) 生型鋳造 球状黒鉛鋳鉄(FCD450) 黒鉛球状化剤の残渣。球状黒鉛化処理温度、出湯温度を上げました。
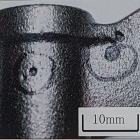
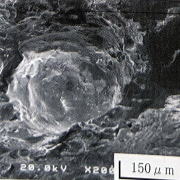
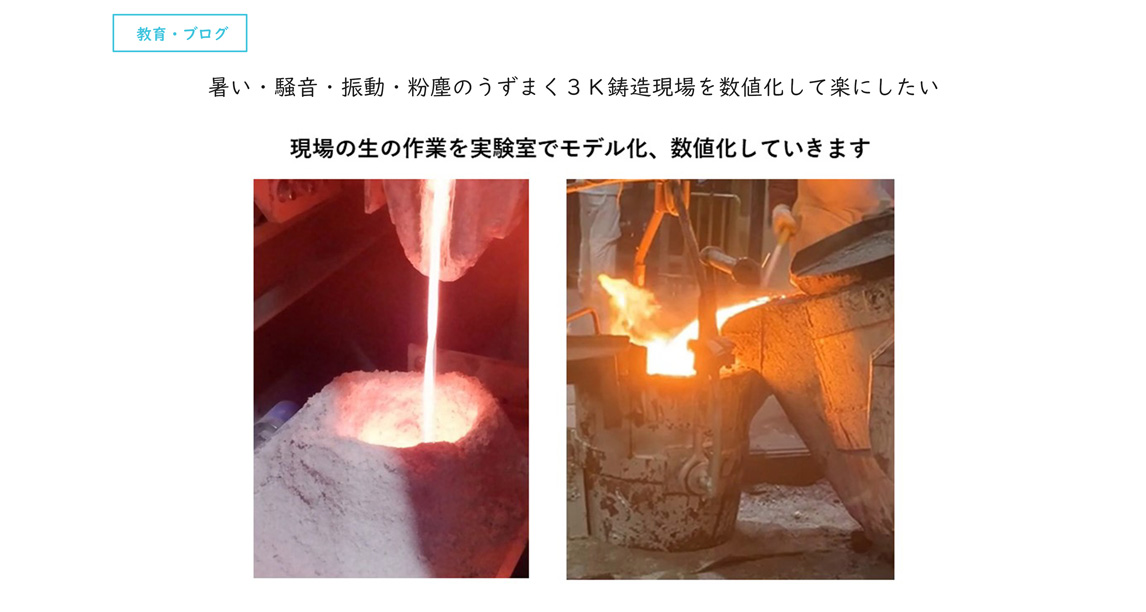
ミクロ偏析、マクロ偏析、気孔欠陥、高温割れ等について説明しています。
参考図書として
● 参考図書の紹介
・「鋳造欠陥とその対策」(日本鋳造工学会)
・「基礎から学ぶ鋳造工学」(日本鋳造工学会)
・「大学講義シリーズ24 溶融加工学」(コロナ社、大中逸雄・荒木孝雄 共著)
・「アグネ技術センター 鋳造伝熱工学」(新山英輔著)
※押湯について詳しく書いてあります。
鋳物の技術史①
金属は、常温・常圧ではほとんどが固体で、展性や延性に優れ、光沢があり、電気・熱をよく導き、削ったり、孔をあけるなど、機械で加工しやすい性質を持っています。銅は古くなると表面が酸化しますが、新しい状態では、きらきらした金属光沢を持ち、金や白金は酸化されにくく、いつまでも輝いているので、貴金属と呼ばれています。
金属元素は、自由に動き回る、自由電子を持つため、電気を伝えたり、光沢を放つなどの、特徴が出てきます。多くの金属は、体心立方格子、面心立方格子、最密六方格子という、密度の高い結合をしているのが普通です。
● 金・銀・銅
金銀銅が、人類が初めて意識して接した金属かもしれません。その中でも、特に金は、川床に輝く、小さい黄金の粒のように比較的純粋な状態で地上近くで発見された自然金で、集めて叩き伸ばして、腕輪などの装飾品が作られました。自然銅や隕鉄を拾い集めて、金と同様、鍛圧成型の過程を経て利用されていましたが、やがて火を使って鉱石を精錬し、鋳型に流し込むようになりました。(鋳造)
渓谷の川床に輝く砂金としては、中東の、鉱物資源を埋蔵する山岳地帯をかかえたチグリス・ユーフラテス川にはさまれた肥沃な三日月地帯が有名です。その西方、地中海に浮かぶキプロス島は、銅鉱石が豊富で、銅をラテン語でcuprum、英語でcopperと言いますが、キプロス島の名前に由来しているということです。銅鉱石の一種である孔雀石は、化粧の顔料に使われ、エジプトのクレオパトラのアイシャドーにはキプロス産の孔雀石が使われているそうです。銅も精錬で取り出せます。
金鉱脈は世界に広く分布しますが、日本では銀のほうが金より主役でした。(銀座)世界の貿易決済でも、メキシコの銀が使われていました。銅の精錬はインディアンもしていたようです。木炭で加熱すると700℃位の温度で、容易に還元できました。
● 青銅の発明
銅に少量の錫を混ぜると、銅よりも硬くて有用な合金になることが、B.C.3000年より少し前に発見されたようです。銅の融点は1000℃以上ありますが、錫を混ぜると融点が下がり、700~900℃で溶解します。流動性もはるかに良くなりました。さらに鉛を5~10%加えると粘性が激減し、込み入った鋳型に注ぎやすくなります。中国の初期(商代、B.C.1600~B.C.1000)では、坩堝(るつぼ)による溶解の記録があります。
エジプトでは、ナイル川のほとり、テーベの墳墓から出土した壁画に足踏みふいごで風を送り、鋳型に青銅を流し込んで扉を作る様子が描かれています。(B.C.1500頃)漢の時代(B.C.206~B.C.220)になると竪炉が使われていたようです。秦の始皇帝の墓で発見されたものを集めた、西安の兵馬俑博物館には、青銅製の馬車が飾られています。(B.C.200年頃)食事を作る道具や楽器等、生活必需品に多く使われました。
● フイゴの発明(送風機構) 鉱石から金属を溶かし出すためには、高温を保つ必要があります。そのために空気を送風しなければならないのですが、B.C.2000年頃にメソポタミアやエジプトでフイゴに関する記録が残っています。やがて、足踏み式のたたらへ発達しました。日本の弥生時代前期末(B.C.200~B.C.100)には、メソポタミアや中国大陸では、銅や鉄の溶解が活発で、炉は坩堝型から竪型炉へ。、送風は自然通風の利用から始まり、革ふいごから箱ふいごへと進んでいたようです。そして、足踏み式の踏鞴(たたら)が登場しました。この方式で、江戸時代まで続きました。
● 炉と鋳型
粘土で作った古代の土器炉は、B.C.6世紀には石と粘土で作った製鉄炉になりました。鋳型は、片面の開放鋳型から、密閉鋳型、組合せ鋳型、中子、蝋型と進化しました。8世紀中頃の奈良東大寺の大仏鋳造では、日本初の竪型炉である、こしき炉に関する記録があります。米を蒸す器(甑:こしき)に似ているので、こしき炉と呼びます。
鋳型は砂型と金型に大別され、砂型は粘結剤の種類や硬化法によって、生型、無機・有機自硬性鋳型、シェル型、ガス硬化鋳型などに分類されます。粘結剤を使わずに減圧して固めるVプロセス、マグネットモールド、凍結鋳型、石膏型、セラミックモールド、蝋やワックスを使うロストワックス法、発泡ポリスチレンを使う、消失模型鋳型があります。自動車関連鋳物のような、大量生産品については、高速化・自動化が進んでいるため、ランニングコストで優位な生型造型法が有利ですが、小・中ロット生産の分野では、Vプロセスの特徴とメリットが生きてくるということです。
砂型は近代に西洋から導入された二つの流れがあります。一つはフランス流の粘土の成分が多い「真土(まね)型」、もう一つは、粘土の少ない釜砂(ホロ砂)を焼き固めたイギリス流の「ホロ砂型」です。真土型は日本で古来から伝わる方法でもあり、細い粒(100~150メッシュ)の珪砂や山砂が用いられています。800~900℃に焼成して使います。粘土の主成分は、SiO2、Al2O3、そしてFe2O3です。奈良時代の記録が残っています。
中子には、削り中子、挽き型中子、模惣中子、川砂挽き中子、肉張り中子などがあり、製品の大小、肉厚、数量によって、中子の形状や抜け勾配が選択されます。日本の工芸品に使われてきた、伝統的な蝋を使う蝋型には、蜜蝋や松脂が用いられます。
溶湯と鋳型表面との直接の接触を避け、焼着を防ぎ、鋳造品の鋳肌を平滑にするために塗型剤が使われます。塗型剤の種類(砂型、Vプロセス用、焼失模型用、金型用等)があります。塗型剤の基材、無機燃結剤、、有機燃結剤、溶剤で分類されます。塗型剤の基剤には、ジルコン(ZrO2・SiO2)、マグネシア(MgO)等の耐火性の粉末が使われます。
● 鉄の誕生 青銅技術は、錫が高価なため、支配階級に限られていましたが、鉄の溶錬技術が発明されたとき、金属の使用が一気に広まりました。最初は隕石の鉄が使われ、やがて、砂鉄をや鉄鉱石を還元するようになりました。(700~800℃→1000~1150℃)炭素を除いて、硬くて強靭な鋼にする技術や、焼入れ(熱処理)の技術が加えられました。鉄器が始めてつくられたのは、B.C.2500年頃で、B.C.800年頃から、メソポタミア地方で農具としてさかんに利用され出しています。B.C.200年頃、秦の始皇帝は鉄の農工具作りに力を入れ、耕地を開拓し、民政を安定させています。鉄に炭素を吸収させたり、高温に熱してから急冷して(焼入れ)、性質を変える熱処理が開発された結果、銅や青銅よりもはるかに優れた性質が得られました。隕鉄にはニッケルが多く含まれます。中国での特徴は、鐘や鋳像に青銅でなく鉄が使われているものが多くあることです。古代のヒッタイト王国(B.C.1700~B.C.1200年頃)はトルコのアナトリア高原で豊富に産出する鉄鉱石から鉄を取り出す技術で栄えました。18世紀にイギリスで起こった産業革命では、高炉で得られた鉄(銑鉄)の炭素を減らして鋼(スチール)が作られ、橋や機械等の頑丈な構造物を作る技術が開発されています。日本の古事記には、日本の国土誕生に関しての、天の沼矛(ぬぼこ)、天照大御神がこもった天の石屋戸の木にかけた鏡や、ヤマタノオロチの尾から出た鉄剣、草薙の太刀のことが書かれています。古来、日本では高炉が導入される前は、主に砂鉄を使った「たたら製鉄」が行われており、現代の高炉で作った鉄と比べて、靭性に富む、良質の鉄が得られるので、今でも日本刀等の原料鉄として欠かせないため、年に数回、たたら炉での製鉄が行われています。
鋳物の技術史②
● 弥生、古墳時代の鏡、江戸時代の魔鏡や柄鏡
法隆寺の南東、奈良県磯城郡田原本町八尾に鏡作神社があり、この鏡作神社を中心に、鏡作麻気(まけ)神社、鏡作伊多神社、石見鏡作神社が散在しています。この地は秦姓の人が多く、天日槍(あめのひほこ)の子孫と称する三宅連と関連の深い土地で、弥生時代には銅鐸が作成され、近くの紫金山古墳では勾玉の模様のある鏡が発見されています。このように、銅剣や銅鐸の鋳造が始まったのは弥生時代とされています。弥生時代に続く古墳時代には鏡や各種の馬具が鋳造されました。平城京跡からは、和同開珎等の銭貨の未完成品が出土しており、平安時代には東国においても青銅鋳物の鋳造品がみられます。
平安時代の鏡は唐の鏡を模倣したものから始まり、11世紀には和鏡と総称される、日本的な鏡の製作が始まっています。現代の鏡は、ガラスの裏面に水銀などを塗っていますが、これは明治時代以後のことで、それまでは、主に青銅で作り、表面を磨いてから、スズアマルガム(スズと水銀との合金)を塗って光らせていたそうです。室町、江戸時代には、持ちやすいように、取手をつけた柄鏡が作られました。
鎌倉時代、中世の鋳物師(いもじ)は、商工未分離の手工業者から組織化が進み、河内から全国に散らばり始めました。(12~13世紀にかけて鋳造された81口の梵鐘のうち、約62%に当たる50口が河内鋳物師の作品だそうです)室町時代は流通が活発化し、城下町に定着して領主と特権を保証される鋳物師が出てきました。16~17世紀は、宮廷蔵人所の真継家による鋳物師の支配(免状を与えるなど)があったことが知られています。鋳造関係の工人には、鉄と青銅を扱う鋳物師と銅を扱う銅細工(あかねざいく)がいました。銅細工は、仏具や建築に関わる装飾品を扱い、彫金や鍍金(メッキ)も行っていたようです。
中世末期から近世にかけては、江戸、武州川口、京都、大阪、高岡、新潟県の柏崎等に多数の鋳物師が住み、大きな生産地になっていました。需要が限られていたために、新規の鋳物師の参入は禁止されていて、家業は男氏一人にのみ相続が認められました。
江戸時代の青銅の鏡の内、裏面の模様や凹凸が映し出される魔鏡が発見されています。篦(へら)を使って、外型の表面に模様や文字が描かれますが、文字をはじめ、すべてが逆さになっているので、この技法は大変な熟練を要します。貨幣には型押し、鏡には江戸時代中期以降は、踏返しと呼ばれる型押しの技法が使われています。
● 古代の鋳鉄鋳物の代表、鍋や釜 青銅と比べて鋳鉄鋳物の代表である鍋や釜は錆びやすく、すぐにリサイクルされるので、残っている資料は少なくなります。中世においては、鋳物師が生産を担っていました。鎌倉時代に入り、茶の湯の興隆に伴って、釜が鋳鉄鋳物で作られるようになりました。なお、古事記に出てくる天児屋根命が日本で初めて鍋釜を用いたとも伝えられます。鍋や釜の鋳造には、”枚”という独特の単位が用いられていました。
鋳物の技術史③
● 鋳鉄佛、鋳鉄銭、梵鐘 鋳鉄佛、鋳鉄銭、梵鐘などに鋳物師の技術が使われています。 例えば、蝋の模型には、彫刻型、蝋挽法があり、型込め・焼き流しで鋳型を仕上げます。梵鐘の竜頭などは木型が使われ、陶模という粘土で原型を作り、焼きしめた雄型とそれを鋳物土に押しあてて雌型を使う方法、中国の土に埋める地坑造型陶範法が奈良の大仏には応用されています。仏像に関しては鋳込み後の仕上げが重要です。京都の左京八条三坊、鎌倉の今小路西、堺の環濠都市に銭の鋳造遺跡が見られます。
● 鋳鉄鋳物の発展
鋳物業は、常に火を使う職業なので、火事の危険性から城下町のはずれの風下の立地が望まれました。鋳型の乾燥や炉のためにも、地面が湿っているような土地は好まれませんでした。近世の鋳物業は、御鋳物師と呼ばれる親方の下に職人達がいてたたら師が8~12人ほど臨時に雇われていました。鋳物師の家は大きな敷地でした。
日本と欧米の鋳物業を比較すると、鋳物業の歴史は中国や日本の方が古くなります。異なるのは、イギリスでは最初から鉄の大量生産、大量利用を目指していたことです。日本の近世は、熱源としての木炭、鋳型に用いる川砂と粘土の確保が重要な課題で、産地は鉱石の産地(主に中国地方)で、市場に近い城下町や港湾に集まっていました。これはイギリスでも同じでした。しかし、イギリスの生産量は日本とは比較にならないほど大量で、その結果、イギリスでは多くの森林が失われ、木炭製鉄は禁止された場所もあり、イギリスの製鉄業は、ダービーによるコークス法の発明まで、木炭を求めて移動せざるを得ませんでした。
鋳鉄鋳物の生産量が飛躍的に伸びたのは、たたら製鉄に代わり、産業革命の生んだコークス高炉によります。ねずみ鋳鉄が45%、球状黒鉛鋳鉄が20%、ダイカスト10%、鋳鉄管10%。イギリス、バーミンガムの北西60kmにあるアイアンブリッジ(1779年)がその象徴です。全長50m、橋高20m、幅7.2mで、世界遺産に登録されています。(成分はC(炭素)3.25%、Si(ケイ素)1.48%、Mn(マンガン)1.05%、P(リン)0.54%、S(硫黄)0.037%)一方、日本では、鉄は、大砲の砲身の鋳造から始まり、現代では、自動車用が42%、一般産業機械18%、鋳鉄管8%です。日本でも、木炭を熱源とする小型の甑炉で生活用品、梵鐘などが作られていましたが、江戸時代の末期のアメリカの開国要求を受け、国防の必要から大砲の製造が活発になり、反射溶解炉(韮山の炉が代表例)、鋳鉄溶解炉のキュポラ(長崎が初)が稼動するに到りました。幕末には、不景気によって産地の中には困窮するところも出てきました。明治維新後は、従来の特権も失われ(真継家も特権を失います)、鋳造技術も変化しました。鋳型は焼型法から生型法へ、送風も人力のたたらから、蒸気機関、電力、モーターへ、原材料も和銑から輸入銑、高炉銑へ、燃料も木炭からコークスに変化しました。製品も、日用品から機械部品が中心になり、大都市や市場の近い東京、大阪、川口、桑名等が産地として栄えました。
鋳鉄は、ねずみ鋳鉄、または、白鋳鉄とも呼ばれ、Fe(鉄)、C(炭素)、Si(ケイ素)から構成されます。微量のS(硫黄)、Mn(マンガン)、P(リン)も含まれています。2~5%と比較的高い炭素含有量があります。鉄のもう一つの加工法である鍛造は、鋳造とは早くから分離し、軟鉄に刃になる部分だけ少量の鋼鉄をつける日本独特の方法を発展させてきました。鍛冶師と呼ばれる職業で、鋳物師と比較して小規模でも可能でした。
● 非鉄金属について 日本のアルミニウム合金ダイカスト生産量(約46万トン)の内、約95%はADC12です。Ai-Si共晶に近い組織を基本に、Cuが1.5~3.5%添加された合金で、鋳造性や機械的性質に優れた、バランスのとれた材料です。アルミニウムの融点は約660℃です。
鋳物の技術史(人物)
先人の偉大な智恵と功績に感謝し、名前(敬称略)、卒業大学、功績について並べています。(一部のみ、順不同)
2022年、日本鋳造工学会は90年目を迎えました。
1932年(昭和7年)5月29日に設立され90周年にあたり、特別講演会で沿革が紹介されました。「設立の目的」(講演会の趣旨をまとめたものです)古来の日本の鋳造技術は立派な技術であるが、工芸品、家庭用品に限られていて明治維新後の機械鋳物の技術はもっぱら英国・フランスの海外技術に頼っていて、十分に日本の技術として取り入れられていない。機械鋳物(品質・形状寸法が最も重要とされる)軍備拡張のためには、日本の技術では出来損ないが多い。日本の若い技術者に鋳造の神髄を伝え、科学的知識を与えて、合理化を図るために学会を創立したということです。創設当時は「日本鋳物協会」でした。満州事変の頃です。
▼ 横にスクロールしてください。
名前 | 卒業大学 | 功績 |
---|---|---|
草川 隆次 | 早稲田大学 | 鋼、鋳鉄の研究 |
堤 信久 | 早稲田大学 | 戦前は、軍艦・兵器鋳物の試作。鋳鉄鋳物、キュポラ、アーク炉などの溶解設備の研究 |
大和田 利郎 | 東京大学 | 金属の固体-液体間拡散、球状黒鉛、鋳鉄の生成機構のシミュレーション |
長岡 金吾 | 北海道大学 | 球状黒鉛鋳鉄、鋳鉄の成長理論、Fe-C系、Fe-C状態図 |
中村 幸吉 | 早稲田大学 | ミーハナイト鋳鉄・ねずみ鋳鉄・応力・ひずみ曲線、キュポラの設計 |
岡本 平 | 大阪大学 | 特殊鋼、圧延鋼材、白鋳鉄 |
牛山 五介 | 秋田鉱山専門学校 | 可鍛鋳鉄、反射炉、電気炉、キュポラ |
西山 圭三 | 旅順工科大学 | 造型砂、鋳型、ダクタイル鋳鉄、シェルモールド鋳型 |
多羅尾 光一郎 | 早稲田大学 | 鋳鋼、鋳鉄、鉄道車両用鋳物 |
松田 政夫 | 大阪大学 | エンジン鋳物方案、シリンダーブロック、キュポラ、湯口方案、押湯 |
杉山 清 | 日本大学 | フルモールド法、銑鉄、黒鉛球状化したダクタイル鋳物 |
足立 恒 | 名古屋大学 | 金型鋳造、ねずみ鋳鉄、川口鋳物工業共同組合 |
山本 治利 | 東北大学 | ミーハナイト鋳鉄、鋳鉄、ショウプロセス、HBバレル、高いクロム鋳鉄など |
納谷 善郎 | 早稲田大学 | FCD球状化 |
長谷川 年充 | 早稲田大学 | 高マンガン鋳鉄、高クロム鋳鉄、溶解炉 |
和気 慎 | 早稲田大学 | ダクタイル鋳鉄、超大型精密鋳造、土木建築開発メソッド、成功方程式 |
宮田 守次 | 茨城大学 | 鋳鉄製鋳型、ダクタイル鋳鉄 |
大橋 明 | 大阪府立大学 | 自硬性鋳型、人工鋳物砂 |
田中 彬夫 | 大阪府立大学 | 砂型遠心鋳造法、金型遠心鋳造法 |
佐伯 和良 | 山梨大学 | シェルモールド・キュポラ、銑鉄鋳物・シリンダブロック |
村田 悦夫 | 大阪府立工業奨励館 | キュポラ溶解、耐火物、電気炉 |
久保田 保 | 愛知県立工業高校 新東工業株式会社 |
シリンダヘッド、造型機、鋳造プラント、自動加工ライン |
片島 三朗 | 広島工業専門学校 | セメント型、生型、ベントナイト、Vプロセス |
青木 正 | 早稲田大学政経学部 | シェルモールド法、鋳物砂再生 |
田村 尚巳 | 横浜国立大学 | FMC法、フルモールド法、EPS模型、3D-CAD/CAM |
櫻山 輝世 | 大阪府立大学 | 鋼塊 製鋼 黒鉛系接種剤 |
雄谷 重夫 | 早稲田大学 | ダイカストAl合金、青銅、結晶成長、アルミ、凝固 |
諸住 正太郎 | 盛岡高等工業 | マグネシウム鋳造合金、航空機エンジン部品 |
大野 篤美 | 千葉工業大学 | 鋳塊、凝固機構、連続鋳造法、OCCプロセス |
大谷 利勝 | 早稲田大学 | 機械学会、光造型法 |
梅村 晃由 | -- | 鋳物の凝固、数値計算、熱・物質移動、流体力学 |
中野 俊雄 | 東北大学 | 粉末冶金、キュポラ、アルミニウム合金鋳物 |
星野 克英 | -- | 電気炉鋳鉄(ダイヤナイト、鋳鉄、航空電装品鋳物、キュポラ(こしき炉)、シェルモールド |
中村 元志 | 東北大学 | 計測鋳造技術、センサーダイカストプロセス |
杉浦 泰夫 | 早稲田大学 | アルミニウム、ベリリウム銅合金、マグネシウム鋳物 セミソリッド・チクソ |
外山 隆 | 名古屋大学 | 鋳造設備、造型設備、作業環境、公害防止、省エネ活動 三現主義 |
関連ページ

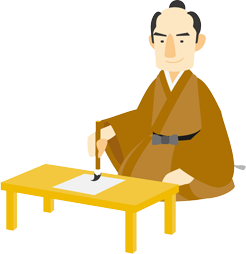
JSCASTのご利用や、受託解析サービスのご利用、資料レンタルなど、 様々な内容をお問い合わせいただけます。まずはお気軽にお問い合わせください。 (5営業日を目安に返信いたします)
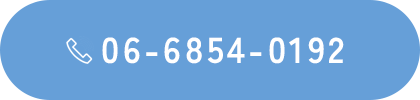
※または代表直通番号(090-3871-0192)へ
おかけください。